Ultrasonic Welding Plastic
Discover what Stelray can do for you
Ultrasonic Welding of Plastic Parts
Ultrasonic welding is one of the most popular methods for joining plastics—given the process is fast, economical, easily automated, and well suited for high-volume production to bond or fasten molded plastic components to one another. Ultrasonic welding also is used to insert metal parts into thermoplastics and polymetric components—or to otherwise fasten pieces made of other materials onto plastic parts.
Commonly understood as a plastic “melting” technique, ultrasonic welding produces a molecular bond by applying high-frequency energy to component parts held together under pressure. During the process, heat generated by friction causes severe plastic deformation limited to the application point. Vibrations applied at the joint interface create a molecular bond or weld, once cooled—without otherwise altering the base materials.
Ultrasonic welding is deployed across a wide range of applications, including the manufacture of high-precision parts commonly used in the automotive, electronics, appliance and medical device industries.
What are the advantages of ultrasonic welding plastic?
Ultrasonic welding offers several advantages over traditional welding or bonding methods. It produces clean, precise welds without the need for additional materials, resulting in a seamless finish with minimal aesthetic impact. Additionally, the process is fast, typically completing a weld in a matter of seconds, making it highly suitable for high-volume production environments. Moreover, ultrasonic welding is capable of joining dissimilar materials and complex geometries, providing versatility across a wide range of applications in industries such as automotive, electronics, medical devices, and packaging.
Common Ultrasonic Welding Joints
1. Butt Joint
-
One surface is flat while the other has a triangle shape. Keeping the triangle point as sharp as possible maximizes energy transfer.
2. Step Joint
- The mating surfaces have a stepped design that minimizes lateral movement while the triangle point presses against a flat surface. (This simplifies part location for assembly.)
3. Criss-Cross
- Both surfaces have energy directors but are aligned perpendicular to one another. This yields stronger welds but can also produce a lot of flash. To achieve an air-tight seal configure the crossing energy directors as a sawtooth.
4. Textured Surface
- Texturing the non-energy director surface is an effective way of increasing weld strength.
5. Perpendicular
- In this design the energy directors run perpendicular to rather than parallel with the joint faces. This reduces flash.
6. Interrupted
- Energy directors are kept short. This reduces the energy needed to make the weld.
7. Chisel
- A variation of the step joint, by putting the energy director along the mating wall enables welding of thinner sections.
8. Tongue & Groove
- The energy director is on a raised tongue that fits into a groove in the mating part. This provides good alignment of the two parts and minimizes flash.
To learn more about the common Ultrasonic welding joints, read our blog, “Ultrasonic Welding for Plastic Parts: Design Considerations”
Ultrasonic Welding Material Considerations
Ultrasonic welding works best on plastics that soften gradually over a temperature range. Typically these are thermoplastics with an amorphous structure. Their melting behavior is characterized by a “glass transition temperature” or Tg.
Among the easiest plastics to weld ultrasonically are acrylonitrile butadiene styrene (ABS), and polyphenylene oxide (PPO). In contrast, a semi-crystalline structure makes polyvinyl chloride (PVC), polyesters (PET, PBT), and polyolefin materials difficult.
Ultrasonic welding is easiest when parts being joined are molded from the same material. At the other end of the spectrum are assemblies in which component parts are molded from plastics with different properties. (Note that semi-crystalline plastics can in general only be welded to themselves.)
Gauging the weldability of dissimilar thermoplastic materials entails considering the glass transition temperature (Tg), chemical compatibility and melt flow index (MFI). As a rule, the Tg of two dissimilar plastics should be within 40°F for them to fuse successfully.
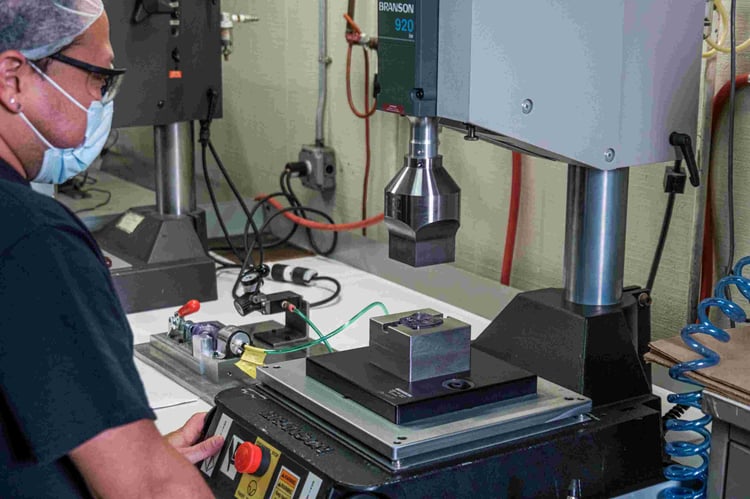
What our team of experts can do for you
Stelray is a full-service company, offering in-house mold tooling, design and engineering support, and custom manufacturing for a variety of plastics-based products. Our clients include top U.S. and international brands such as ITT, Panasonic, Hill-Rom, Hubbell, Sub-Zero and Welch Allyn.
Our facility is ISO 9001:2015 certified to ensure that every project we take on meets all applicable quality requirements. We also are an FDA Registered Manufacturing Facility and compliant with 21 CFR 820 and Good Manufacturing Practices, among other certifications and standards.
All design and manufacture work is done by our team of experts—for a complete custom application. In addition, we offer a range of secondary operations, including pad printing, heat-staking, soldering, assembly and packaging.
Our engineering staff and machine technicians are experienced in a broad range of plastic resins—from commodity-grade to engineering-performance polymers and exotic resins—to help guide you in selecting the best material for your project. Biodegradable plastic resins also are available, when appropriate.
Stelray Plastic Products launched more than 60 years ago with the mission of meeting customer challenges with partnership-driven solutions. Our experience with precision plastic injection molding services and plastic resins provides us with a wealth of knowledge and expertise to deliver whatever components your project demands.
Our specialty production shop is equipped to take on short-, long- and mid-volume runs, and offers clean and white room services for medical, dental and bioscience applications.
To learn more about us and the work we do, including our ultrasonic welding capabilities, please get in touch. We’re here to help you.