Draft Angles in Part Design for Plastic Injection Molding
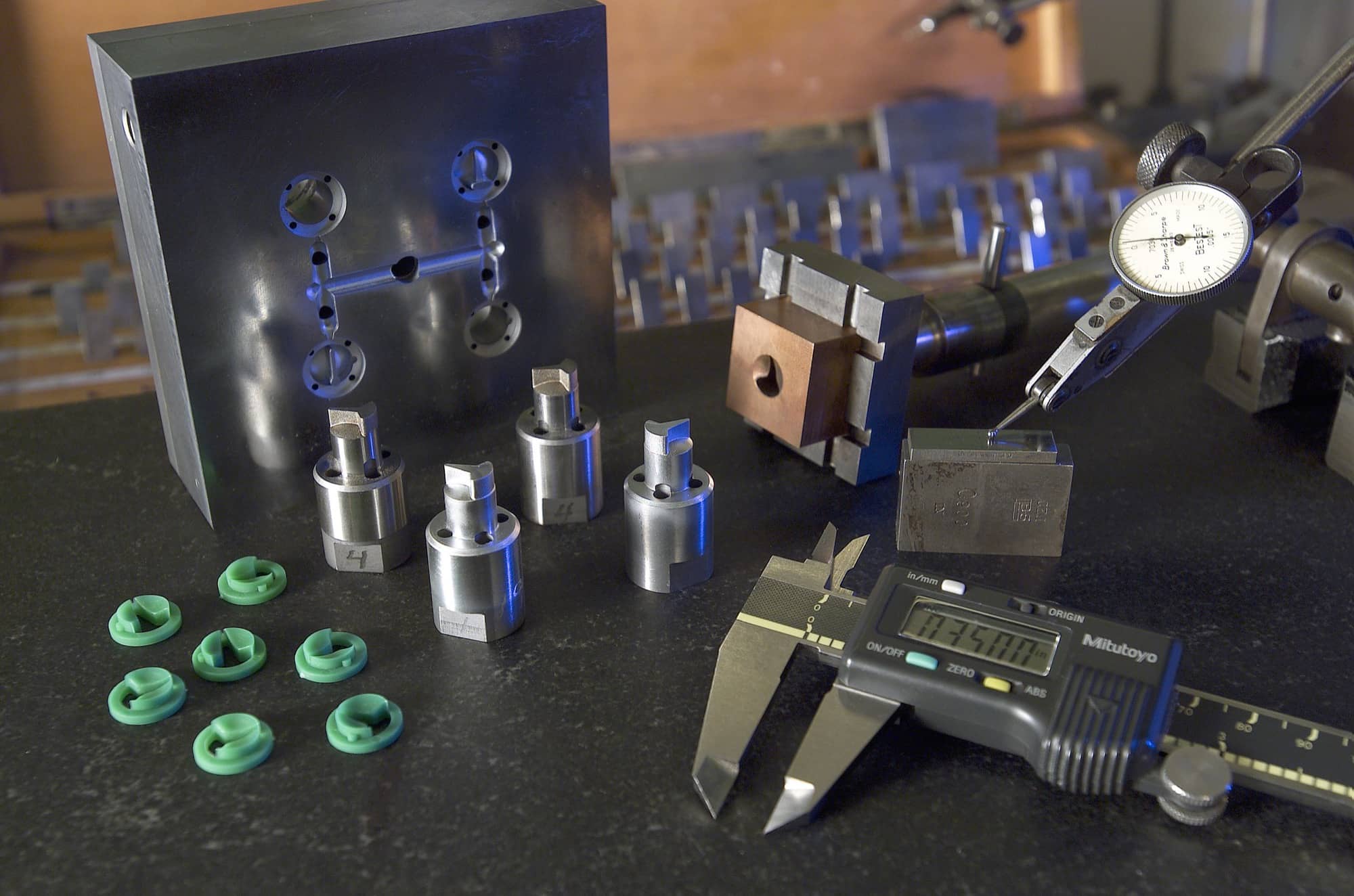
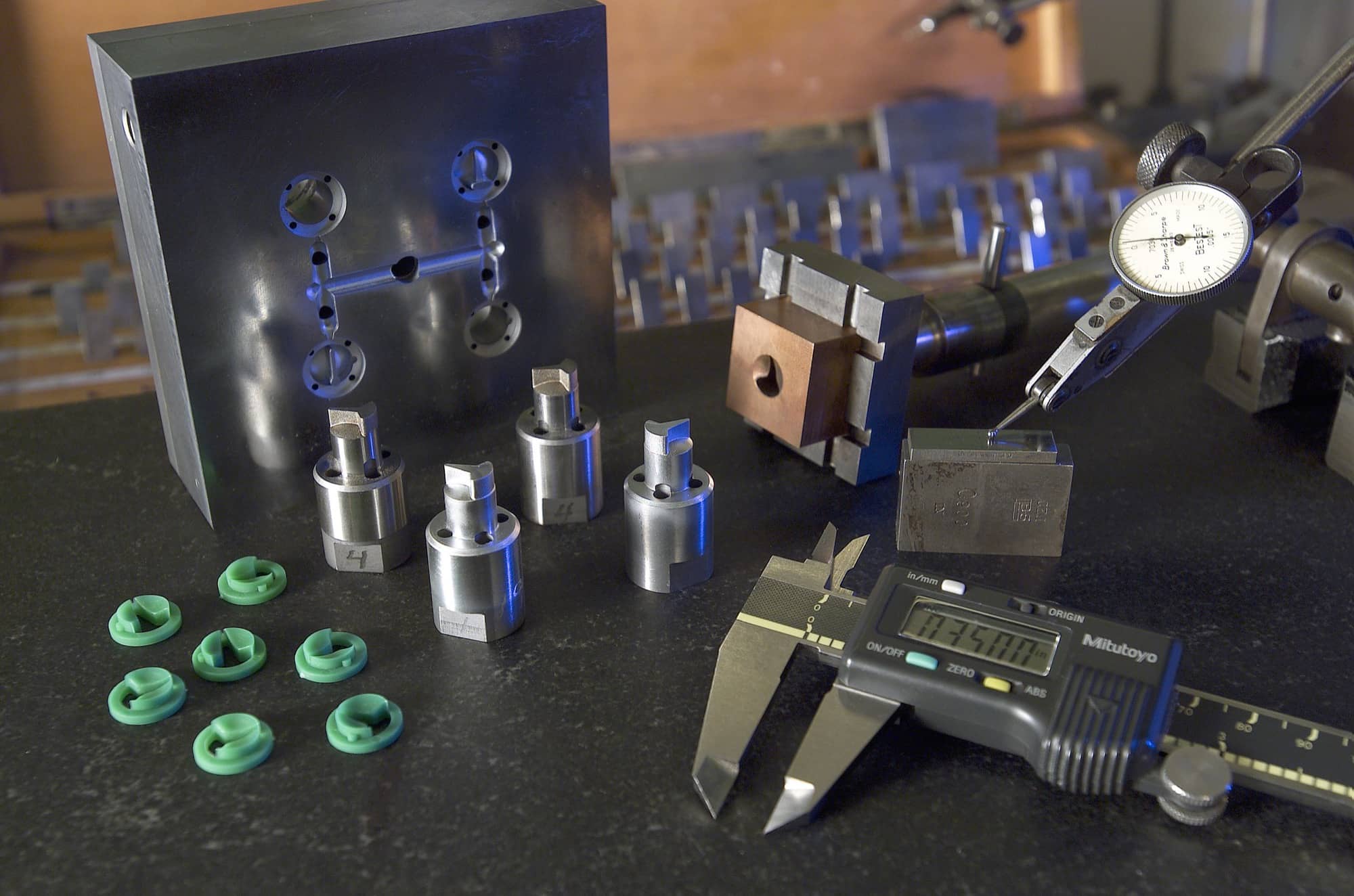
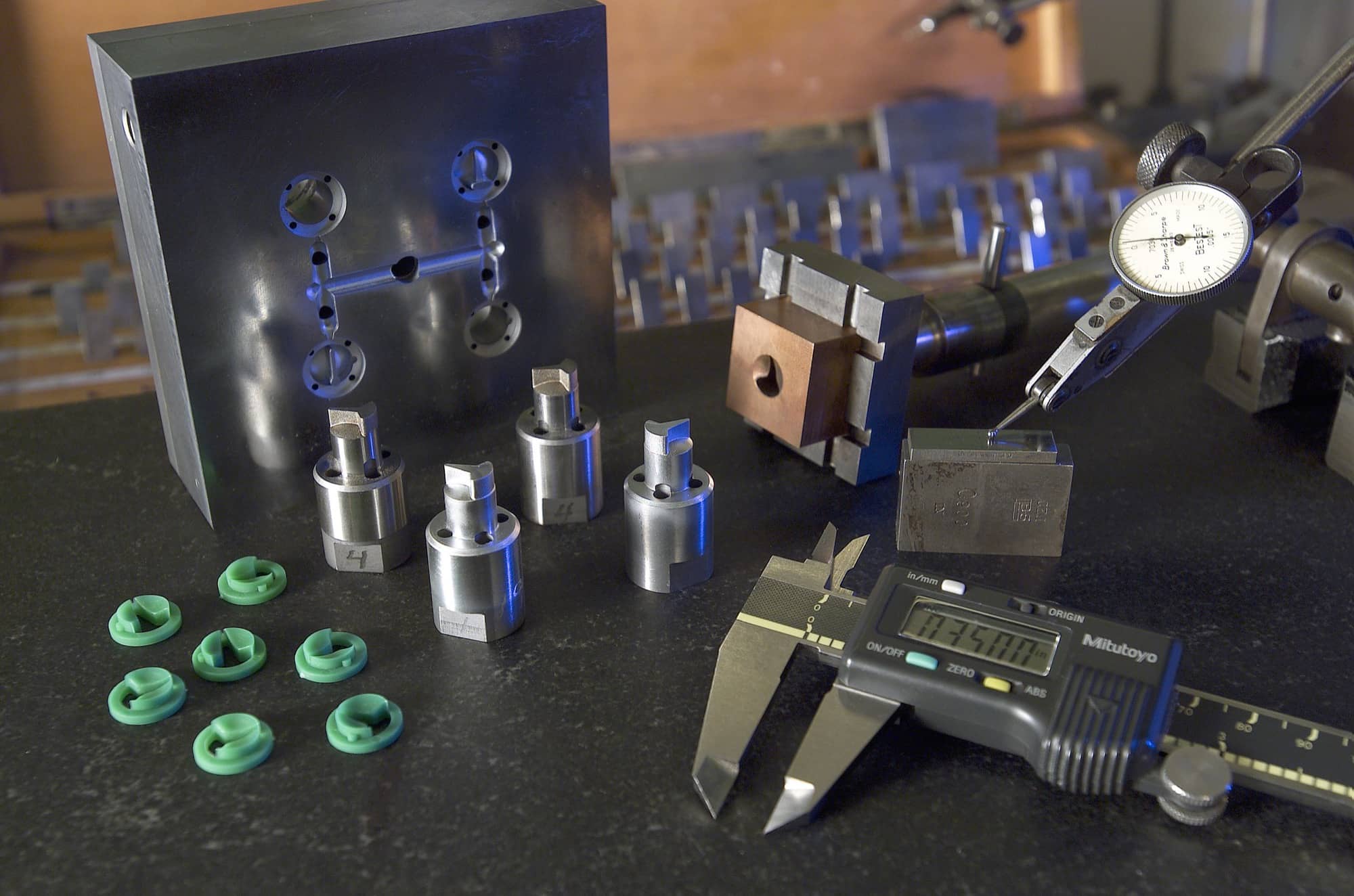
Why draft angles are important in part design for plastic injection molding
Injection molding is a fast and economical method of mass producing highly repeatable, accurate dimensions and aesthetically pleasing plastic parts – but all of these manufacturing attributes can become an injection molders nightmare if the product is not designed properly and the part hangs up in the mold, it is important conduct a Design For Manufacturability (DFM) analysis your injection molded parts. Shrinkage can pull the plastic tight around raised features, and when that happens the only way to get the part out is to peel it away, leaving a less than optimal surface finish. Cycle time increases, the machine operator gets frustrated and there’s more chance of damaging either the part or the tool. In the case of an automated injection molding process, part ejection problems can bring it to a complete stop.
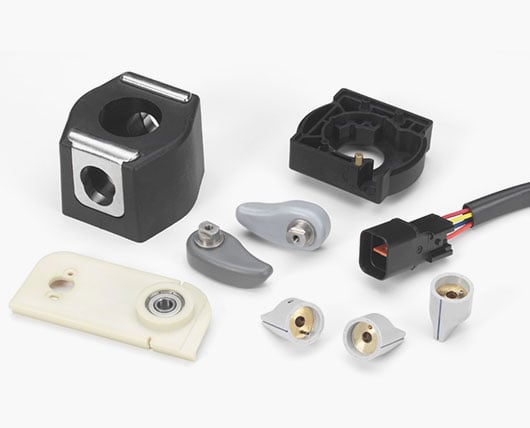
Design engineers and toolmakers aren’t fans of draft angles because they complicate part design and tool manufacture. But without them a part becomes more expensive – maybe even impossible – to produce. Whenever a part is designed for injection molding it’s important to incorporate draft angles.
Reasons to include draft angles for plastic injection molding:
Draft Angle in Part Design and Differential Expansion:
Plastic injection molding melt temperatures are typically around 400°F. That lowers viscosity to where the die fills quickly yet also allows rapid cooling and solidification. Thermoplastics have a higher coefficient of expansion than tool steel, so the parts contract more as they cool and tend to pull away from external walls. At the same time though, they shrink down onto raised internal features.
Designing for Plastic Injection Molding Manufacturing:
Molding variables, such as ejection, cycle times, and production yields, are determined by how the mold tool handles this shrinkage. It follows then that the tooling, and by extension the part, must be designed accordingly. That’s done by incorporating draft angles. Draft angles incorporated into the mold design alleviate ejection issues. A draft angle is a taper applied to a nominally vertical surface. How much taper depends on both the characteristics of the plastic and the functional requirements of the part. Many toolmakers will start out at 1° per inch of vertical height, but then adjust this as necessary.
Draft Angles and Lower Plastic Injection Molding Costs:
Failing to consider what the injection molding process needs in terms of part and tool design leads to higher manufacturing costs. Yields suffer as damaged and defective parts are scrapped and cycle times increase. It may be difficult or impossible to implement automated de-molding.
By incorporating draft angles into part and tool design these problems are reduced, possibly even eliminated. It may complicate your injection molding designs and add to tooling costs, but the result is less headaches for your molder, a better quality part, and ultimately a lower piece price to your business.
Stelray is a full service plastic injection molding company ready to help with your next project.